Blog
Share this
Is ERP Worth the Cost? A Complete Guide to ERP ROI
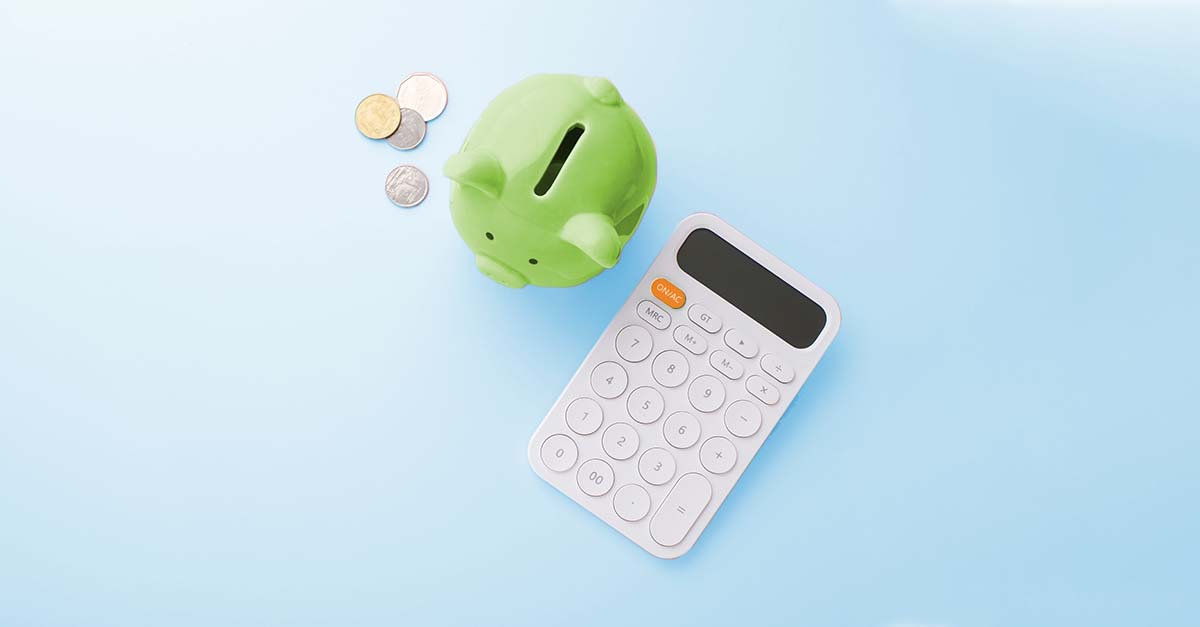
by Carly Caines on August 22, 2025
When you’re shopping for ERP software and see the price tag, it’s natural to wonder, "Is this really worth it?" If you’ve come across ERP quotes that feel higher than expected, you're not alone. Many small to mid-size businesses find themselves in this situation when considering an ERP implementation.
Here's what we’ve found through decades of working in the ERP space: Budget becomes a big hurdle when the value isn’t clear.We also know that ERP isn’t just another software purchase. It’s a long-term investment in how your business runs. And when it’s the right fit, the return can be transformational.
What is ERP ROI?
The ROI (Return on Investment) of ERP is a measure of the value your business gains compared to the cost of your ERP system.
How to calculate the ROI of ERP
Let’s start with this formula:
ROI = (Value of investment – cost of investment) / Cost of investment * 100%
To get a realistic number, you’ll want to look at both your Total Cost of Ownership (TCO) and the measurable benefits. Here’s how that breaks down.
Total cost of ownership
- Software licenses or subscriptions
- Implementation services
- Training and onboarding
- Custom development or integrations
- Ongoing support and maintenance
Measurable benefits
ERP systems deliver savings across three key areas:
1. Displaceable costs
- Lower inventory costs: Better inventory management leads to reduced carrying costs, fewer expedited shipments, and increased inventory turns.
- Reduced labour costs: Automation minimizes manual tasks, allowing your team to focus on higher-value work. For example, one ProjectLine customer eliminated the need to hire an extra full-time role after ERP implementation.
- Reduced days sales outstanding: With integrated quote-to-cash processes, you can speed up invoicing and improve cash flow. One client reduced invoicing time from three months to two weeks.
2. Avoidable costs
- Avoid leasing additional warehouse space by improving inventory turnover.
- Prevent headcount increases or reduce costly overtime through process efficiency.
3. Intangible benefits
- Better decision-making with more reliable data
- Enhanced customer relationships via faster service
- Stronger vendor negotiation resulting in better pricing
- Fewer costly errors and smoother handoffs between departments
You won't be able to catch every benefit in a spreadsheet, but these should help you build a strong case for the value of your ERP investment.
Real ROI from ProjectLine customers
✅Aircom Instrumentation was planning to hire an additional resource in one department. That need disappeared after they went live with their ERP, saving them the cost of an extra annual salary.
✅Nexus Exhibits reduced their invoicing time from three months to two weeks, giving their cash flow a major boost.
✅ATS Scientific has experienced 50% faster processing time for transitioning quotes into invoices, packing slips and other documentation.
How to improve your ROI from ERP
Getting a great return doesnt mean spending more. It means:
- Choosing the right-fit system (not just the biggest name)
- Standardizing processes before you implement
- Starting with core features, customizing later
- Training your team well from day one
- Working with an experienced ERP partner who can guide you through the best practices and help you avoid common pitfalls
Consider total value, not just the upfront cost
If you're experiencing sticker shock, you're not alone. The price tag of ERP can feel daunting, especially when you don't have a clear picture of what you’re getting in return. But once you see the full scope of benefits—from tangible cost savings to business transformation—the investment starts to make a lot more sense.
Want help building your ERP business case? Many companies struggle with how to confidently invest without second-guessing the outcome. We’re here to help with our How to Avoid ERP Buyer’s Remorse Guide below.
Frequently asked questions
How do you calculate ERP ROI?
Use the formula:
(Value of Investment – Cost of Investment) / Cost of Investment × 100%.
Be sure to include savings in time, labor and operational efficiency.
What are the biggest cost savings from ERP?
Time savings, better inventory control, reduced manual entry, faster reporting and improved cash flow. Those are just a few!
How long does it take to see ROI from ERP?
The timeline varies for every business, but many organizations start to notice improvements soon after go-live. With a smooth implementation and strong employee training, returns like sales growth, lower operating costs and productivity gains can start appearing right away.
Is ERP worth it for small businesses?
In most cases, yes. If the system is a good fit, smaller businesses can see significant efficiency gains and scalability without adding to the headcount.
What’s the ROI difference between cloud and on-premise ERP?
Cloud ERP typically offers faster ROI due to lower upfront costs and quicker implementation. But long-term ROI will depend on usage and fit.
Share this
Stay in the Know!
Join other SMEs who receive our monthly ERP insights, tips and best practices.
You may also like
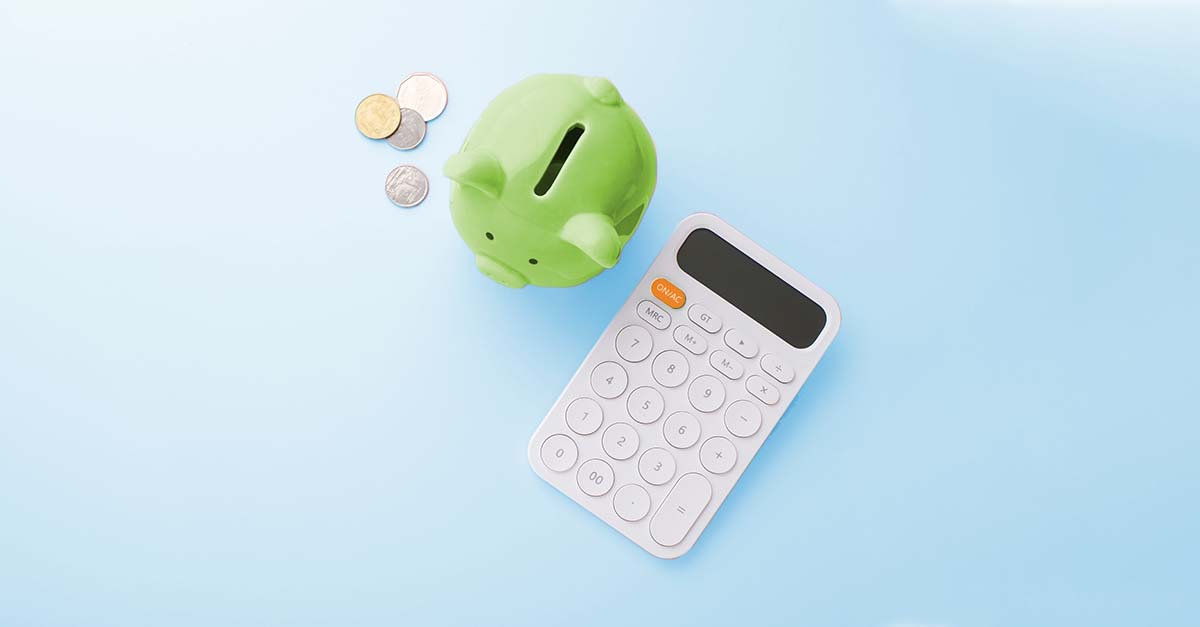
Is ERP Worth the Cost? A Complete Guide to ERP ROI
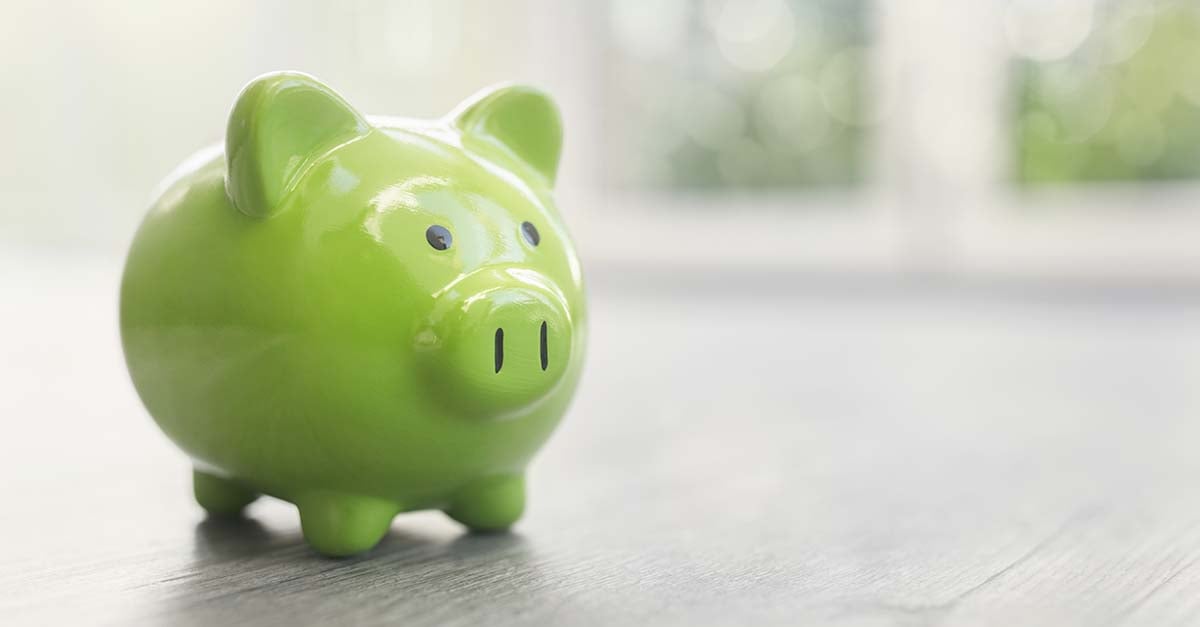
The Complete NetSuite Pricing Guide
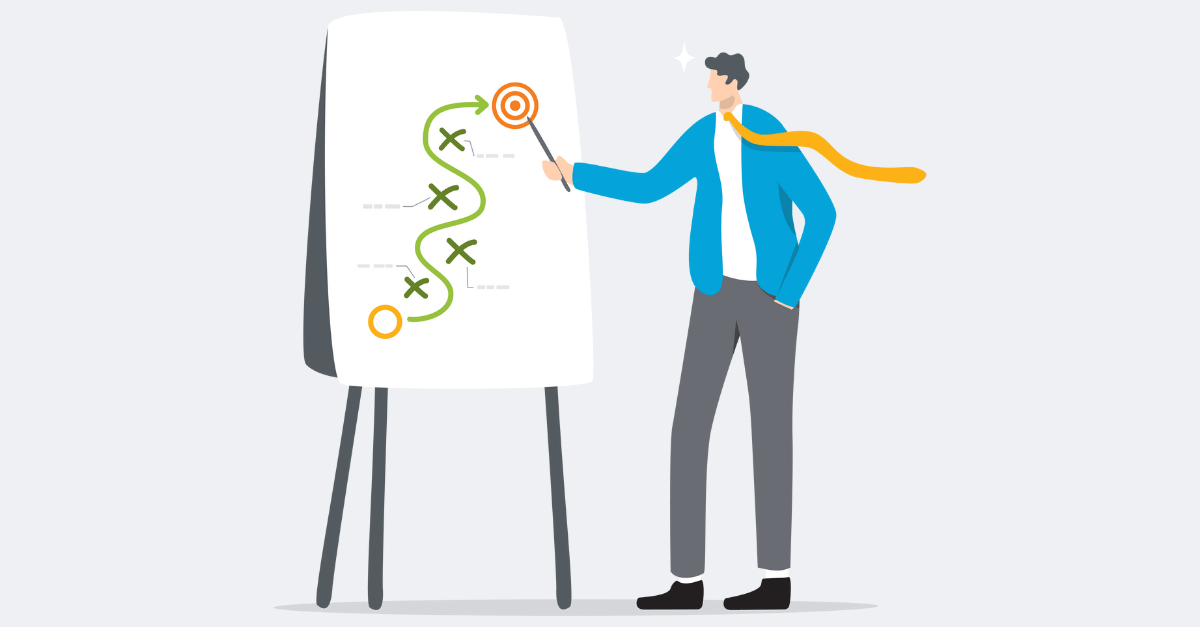