Blog
Share this
6 Steps to Create an ERP Continuous Improvement Plan
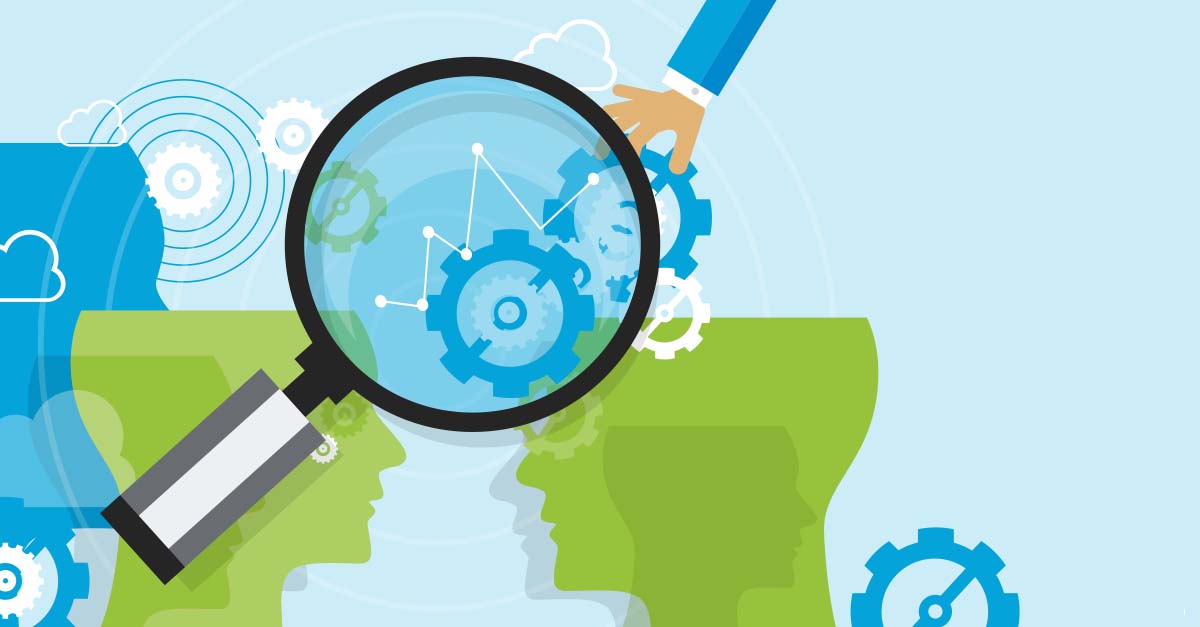
by Jalene Ippolito on September 03, 2020
Your ERP system is a significant investment, in both time and money. Many companies are so focused on go-live as the end point, that they neglect to think about what happens after implementation. While they’ll still see the benefits of their new ERP system, the value of their investment will be limited. These companies tend to react to changes in the business, implementing band-aid fixes or waiting until they need a major overhaul. Not only is this costly, but it takes a toll on your team.
Instead, adopt a continuous improvement mindset. This is a proactive approach where you’re constantly reflecting on your business processes, identifying opportunities for improvement and making those changes to drive consistent growth. Now is the perfect time to make this shift. You’ve spent the last several months focusing on ways to improve the business with your new ERP system. Keep that momentum going by creating a plan to make continuous improvement part of your culture.
Why you need a continuous improvement strategy
Developing a continuous improvement plan helps you maximize the value of your ERP system over time and increase the return on your investment. More specifically, here’s why a continuous improvement plan is a necessary next step in your ERP implementation.
- It’s an extension of your ERP post-implementation activities. During your implementation, you’ll inevitably have a list of ‘nice to have’ items that are out of scope. They’ll provide value in the future but aren’t critical to achieving your project objectives. A continuous improvement plan gives you a way to manage these activities and proactively implement value-add requirements.
- It helps you stay on track. Without dedicated resources and scheduling, your process improvement tasks will fall off the priority list. Forming a continuous improvement committee ensures that you have people responsible for managing these activities and driving your initiatives forward.
- It makes process improvement a priority. As your business changes, your processes and systems need to adapt at the same pace. With a continuous improvement plan in place, you have a structured process to review opportunities, prioritize them and manage the implementation of new functionality or process changes.
- It helps you manage maintenance costs. A proper continuous improvement plan allows you to prioritize, schedule and budget for system upgrades, implementation of new functionality and changes to accommodate new processes.
While we’re focusing on continuous improvement as it relates to your ERP system, we encourage you to develop your strategy more broadly. Remember that people and process drive technology, so that should be the focus of your continuous improvement initiatives. Your ERP system will be central to achieving the improvements you identify, but don’t restrict your view of continuous improvement to ERP alone.
6 steps to create an ERP continuous improvement plan
1. Create your continuous improvement committee
Like your ERP project team, you want a cross-functional group that can provide input from all areas of the business. This committee is actively involved in defining and implementing improvement projects. They’ll be responsible for gathering input from their respective teams, evaluating opportunities, prioritizing initiatives and managing the execution of the changes. Aim for four to six individuals who have a good understanding of the processes in their functional area and have authority to make project-related decisions.
2. Outline a process for evaluating opportunities
First, decide how you want to collect ideas from the organization. Remember that some of the best ideas will come from your employees doing the day-to-day work. Let them know how they can provide feedback. You might choose to funnel everything through the designated committee members from each functional area. Or you could create a committee email address that employees can send suggestions to.
Next, your committee should settle on a method to identify and prioritize opportunities. Be sure to include the impact for each one – what’s the benefit to the company? You may also want a simple measure of complexity – how difficult / costly is the initiative to implement? These factors will help you prioritize and schedule initiatives. The low effort items can be implemented and checked off the list quickly. And for opportunities that require additional investment, you can target a time frame, then secure the necessary budget and internal resources.
3. Consider process first
Your ERP system will be central to many of your improvement activities because it’s core to your operations. But to get the best value out of your system, remember that process should drive the technology. Before implementing new features or functionality, be sure to understand the business need and properly map out the process.
4. Make data-driven decisions
Your new ERP system gives you visibility and data you can trust. Analytics and reporting will give you a good view of what’s working and what’s not, so leverage your information to identify opportunities and measure your improvement.
5. Schedule regular meetings
Like any effective team, you need to regular touchpoints to make progress. Set a consistent schedule with your continuous improvement committee to reinforce that it’s a priority. Following your ERP implementation, you may choose to meet more frequently – at least once a month is recommended. As the post-implementation activity starts to slow down, you can move to bi-monthly or even quarterly meetings. Whatever frequency makes sense for your business, set a recurring meeting in the calendar and stick to it.
6. Communicate progress to your team
For employees, there’s nothing more frustrating than submitting an improvement idea and hearing nothing back from the committee. Include communication as part of your continuous improvement plan. Think beyond the committee and decide how and when you’ll communicate with the organization about the improvements being made, what major projects are scheduled, and the results you’ve achieved from these initiatives. Your people will feel more involved in the process and will be more likely to submit ideas when they see follow-through from the committee.
Share this
Stay in the Know!
Join other SMEs who receive our monthly ERP insights, tips and best practices.
You may also like
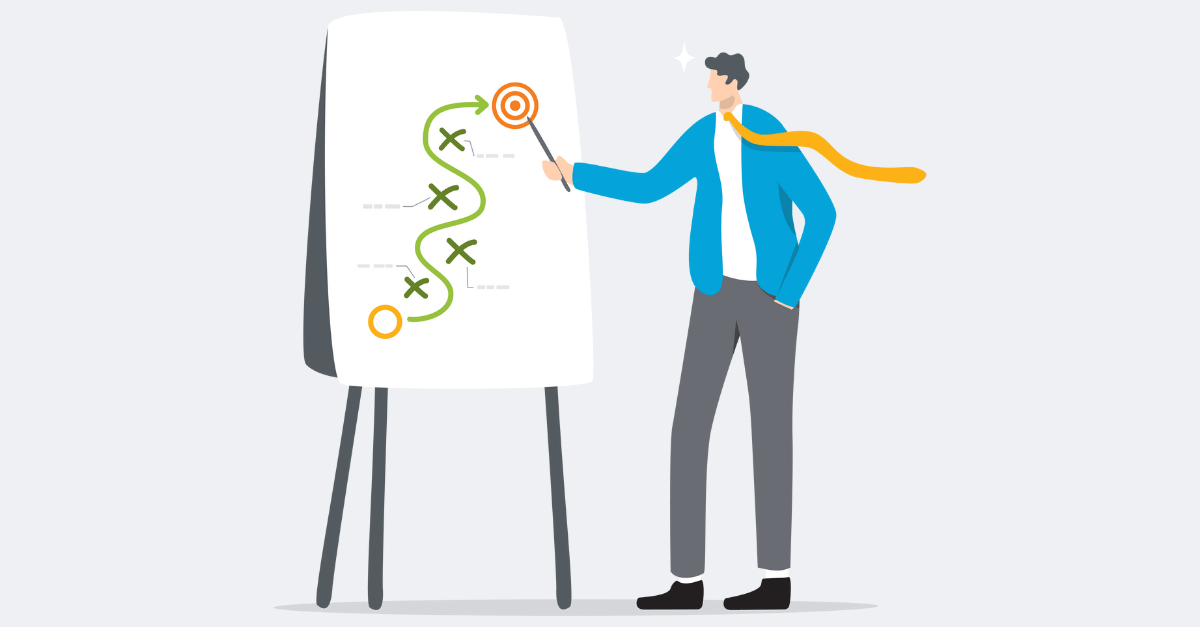
Choosing ERP? Don’t Fall for These Common Sales Traps
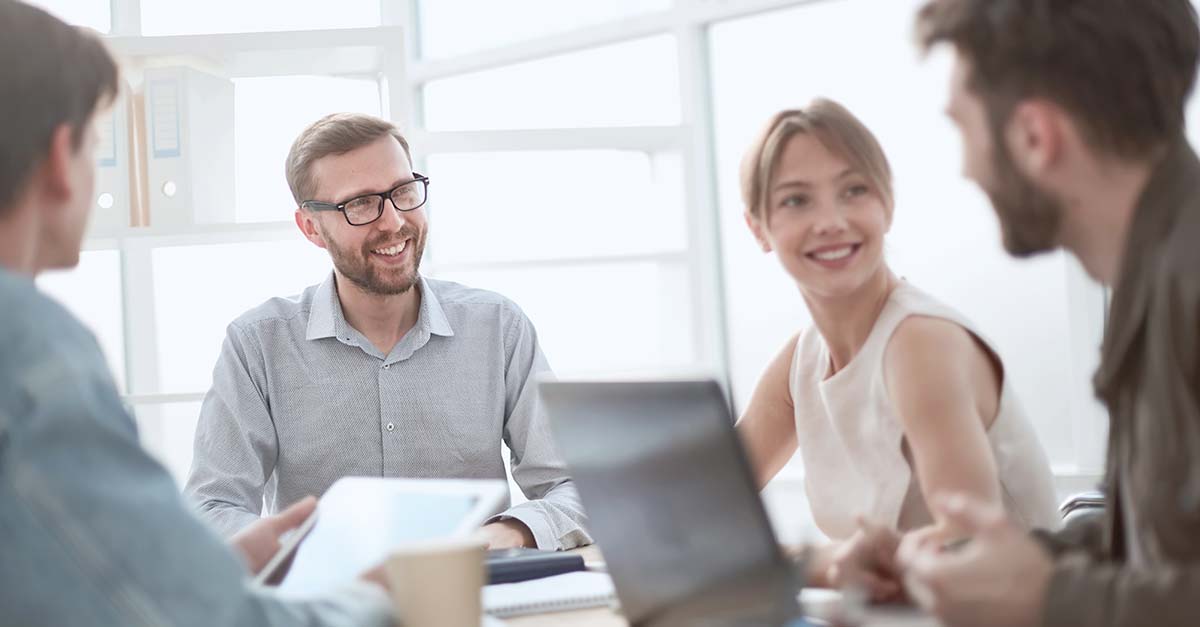
How to Choose the Right ERP Partner
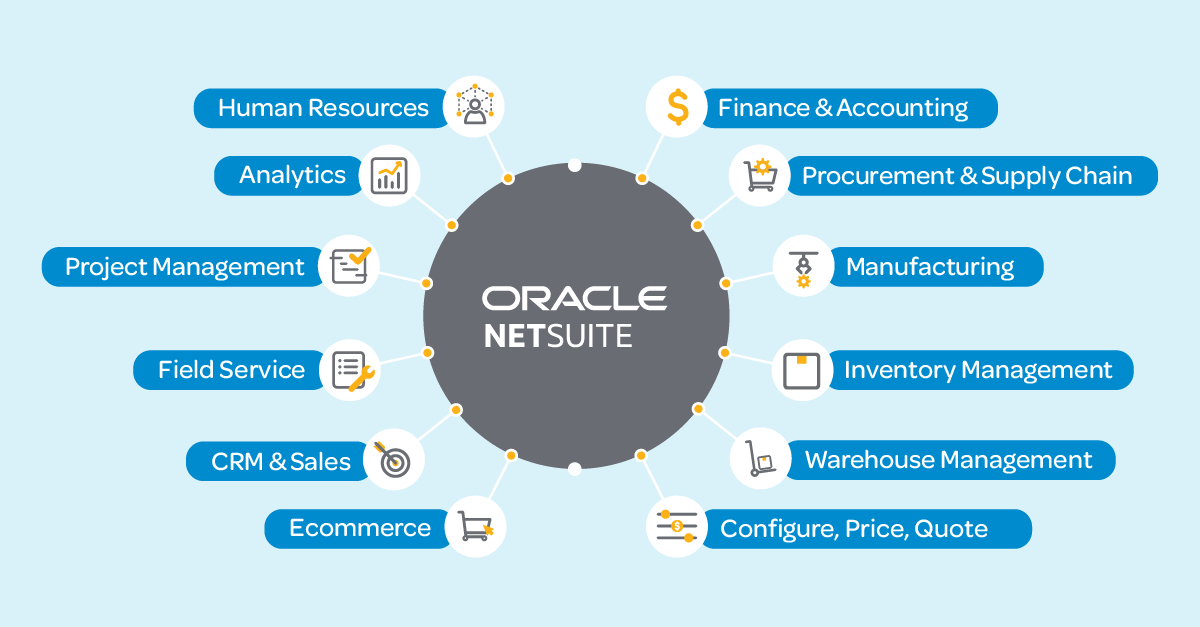