Blog
Share this
5 Key Steps to Selecting an Effective ERP System for Manufacturing
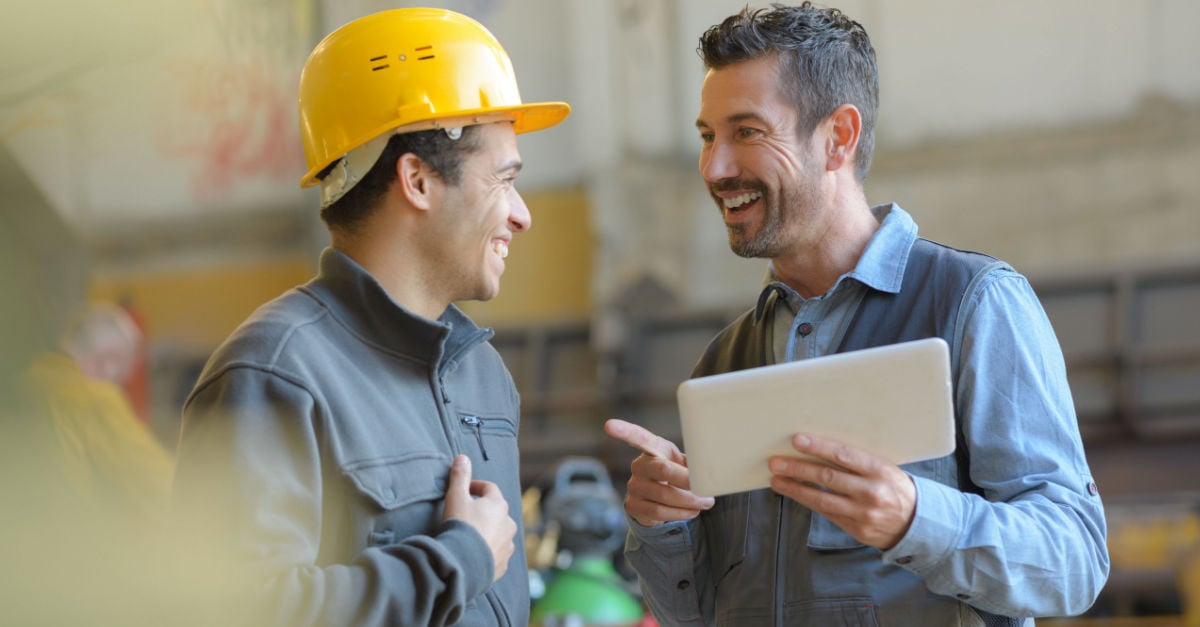
by Jalene Ippolito on May 31, 2023
As a manufacturer, it’s crucial that you have the right materials or components and the optimum resources at any given time to produce and deliver quality products to your customers—all while staying on time and within budget!
A tall ask, you say? Not if you have an effective ERP system to support your operations. An ERP (Enterprise Resource Planning) is critical for your manufacturing company to maximize efficiency and streamline operations.
But many business owners are overwhelmed by the arduous process of deciding on an ERP solution that's right for them. With so many products on the market and the option to build a custom ERP system from scratch, how can you be sure you're making the right choice?
Choosing the wrong ERP software can increase your implementation time by 30%. And most small manufacturing companies don't want an overly complicated solution that takes too long to implement or is too difficult for their staff to learn.
That's why our ERP experts at ProjectLine have put together some practical steps that you can follow to select an ERP system for manufacturing. Read on to learn more.
How to select an effective ERP system for manufacturing
Are you looking to improve your manufacturing business processes?
Whether you want to track goods movement, manage stock levels, forecast demand more accurately, maintain quality or control costs, an effective ERP system helps you optimize processes and run operations more efficiently and profitably, ultimately driving you toward increased business success.
Are you confused about whether to build a software solution from scratch or use an industry-leading solution that can be configured and customized for your needs?
Let's simplify the process, take it one step at a time, and guide you on how to choose an effective ERP system for manufacturing.
Step 1: Identify business requirements and goals
Start with a thorough assessment of your company's needs and challenges and then clearly articulate the goals for implementing an ERP system.
Identify the main pain points you want to address:
For example, is manual BOM (Bill of Materials) management becoming incredibly messy and time-consuming for your staff? BOMs are critical for efficient production. Any errors or inaccuracies in manual BOMs can spell chaos in downstream processes on the shop floor!
If you’re manually reconciling inventory consumed against finished goods, it can result in inaccurate production costing.
Or do you struggle with maintaining an efficient production schedule? If you're still using spreadsheets for production planning, it's easy to fall behind schedule. And that can impact lead times.
Now articulate how this situation should change once you have an ERP system:
For example, with the new ERP, your company can maintain optimal material levels to keep production schedules running efficiently without wasting time waiting for new stock. You can use real-time data to plan production schedules, labor requirements and other expected costs.
Your team can simply enter a BOM into a production order to automatically record item availability, warehouse location and issue method. Automated BOMs eliminate error-prone data entry. Your staff can execute mass changes to components in multiple BOMs simultaneously and the latest version of the BOM is immediately accessible to teams across the organization.
Once goals are defined, you will be in a better position to decide what functionalities your ERP system must have and evaluate the ideal solution to meet your goals.
Have questions about ERP? We've got answers.
Book a quick call with our team to gain clarity and take the next step with confidence. There's no pressure, no obligation—just honest advice to help you make the right decision for your business.
Step 2: Choose the right ERP system and vendor
If you feel you need help with evaluating and selecting the right ERP solution for your company, you're not alone! Many companies find the evaluation process overwhelming.
Here are some questions to help you evaluate your options:
- How well does the system meet our requirements using standard functionality?
- Can it be configured to meet our unique business processes and specific requirements? If it needs customization, what would be the cost and time estimates to execute custom features?
- Can it integrate with my existing tech stack?
- Do I have the resources and technical expertise to execute the ERP system effectively?
- Will it need capital investment into any hardware or digital infrastructure?
- How scalable is the system, considering we want to grow the business over the next few years?
- Is it user-friendly and will our staff be able to adapt to the new system with some training?
- Will the vendor (or partner) provide ongoing support and maintenance?
You can also download our SME Guide to Selecting ERP Software which outlines a proven 5-step process to compare solutions objectively based on business needs, functionality and requirements.
Step 3: Plan the implementation process and timeline
An ERP implementation can be a complex process—a wrong step can send your implementation on the wrong track and prove costly in terms of time and money.
That's why working with an experienced ERP implementation partner is advisable for a successful implementation.
- Ensure your partner has a carefully developed project plan for the implementation with timelines and budget estimates.
- Determine what data you want to carry from the old system and allocate enough time to cleanse, validate and migrate it to the new ERP system.
- Make sure you allocate enough time for thorough testing and dry runs.
Step 4: Configure or customize the ERP system to fit your business needs
Even if you choose a feature-rich ERP software, it may not tick off all the checkboxes on your requirements list. Apart from the out-of-the-box functionalities in the ERP, you may need some customization or integration to get the most out of the solution.
Carefully assess what customizations are essential and how they will impact your project’s cost and timeline. Sometimes, a thoughtful configuration may do the job and save you considerable time and effort.
It takes a responsible and experienced implementation partner to suggest efficient configurations and integrations for building an effective ERP.
At ProjectLine, we work with industry-leading ERP solutions, NetSuite and SAP Business One, which we can configure for your manufacturing business.
If you have specific requirements that aren’t addressed with standard functionality, we'll find and integrate the right third-party solution to fit your needs or build a customized solution if it best fits your requirements.
Book a free consultation call with our ERP experts to learn more!
Step 5: Train employees and monitor the system's performance
Finally, once your chosen ERP system is configured, implemented and tested, you'll want to plan a comprehensive training program for all employees working with the new ERP system.
After all, the best ERP system may not prove effective if you don't train your employees to use it efficiently and to its fullest capability.
At ProjectLine, we include user training in your implementation plan. We conduct training alongside user acceptance testing (UAT) so your team executes processes using real data. This allows them to verify that the system is working correctly and learn by doing at the same time.
Talk to us for comprehensive user training services, including our cost-effective 'Train the Trainer' approach, as well as training to onboard new users or provide refresher training for existing users.
ProjectLine: Helping you choose the best-fit ERP for manufacturing
At ProjectLine, we treat an ERP implementation as an opportunity to improve your manufacturing processes and help you grow.
We optimize your chosen ERP system to meet the unique needs of the manufacturing industry and fulfil your specific business goals.
Our goal is to safely guide you to the technologies and processes you need to run your manufacturing operations smoothly, not just today—but 10 years from now.
Share this
Stay in the Know!
Join other SMEs who receive our monthly ERP insights, tips and best practices.
You may also like
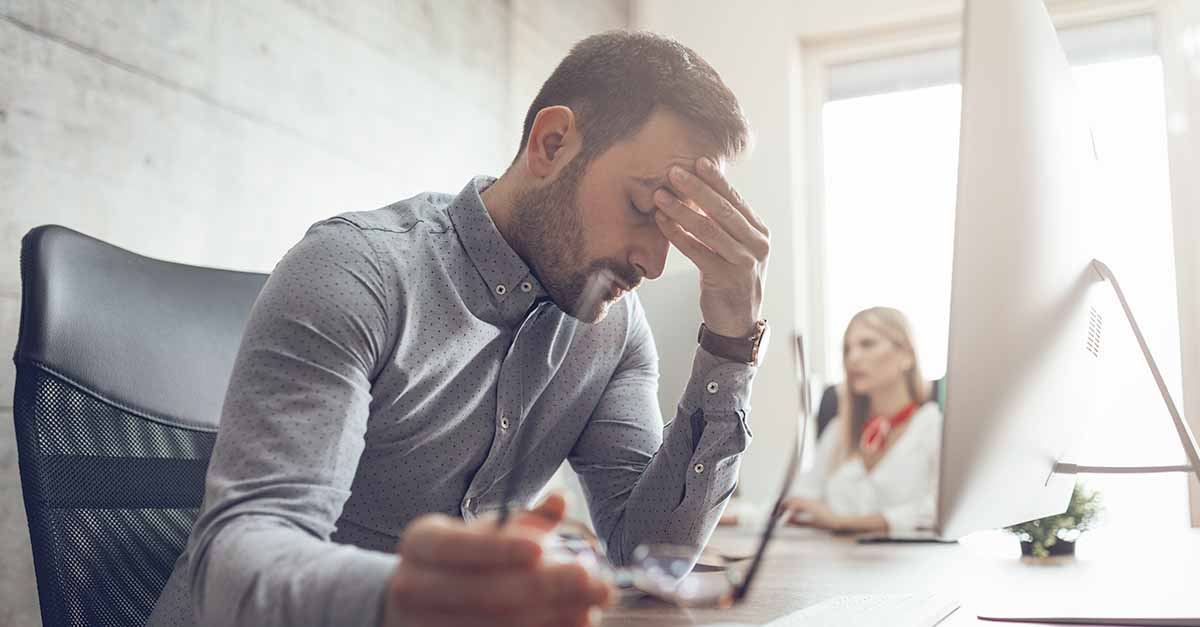
5 Ways Disparate Systems are Costing You
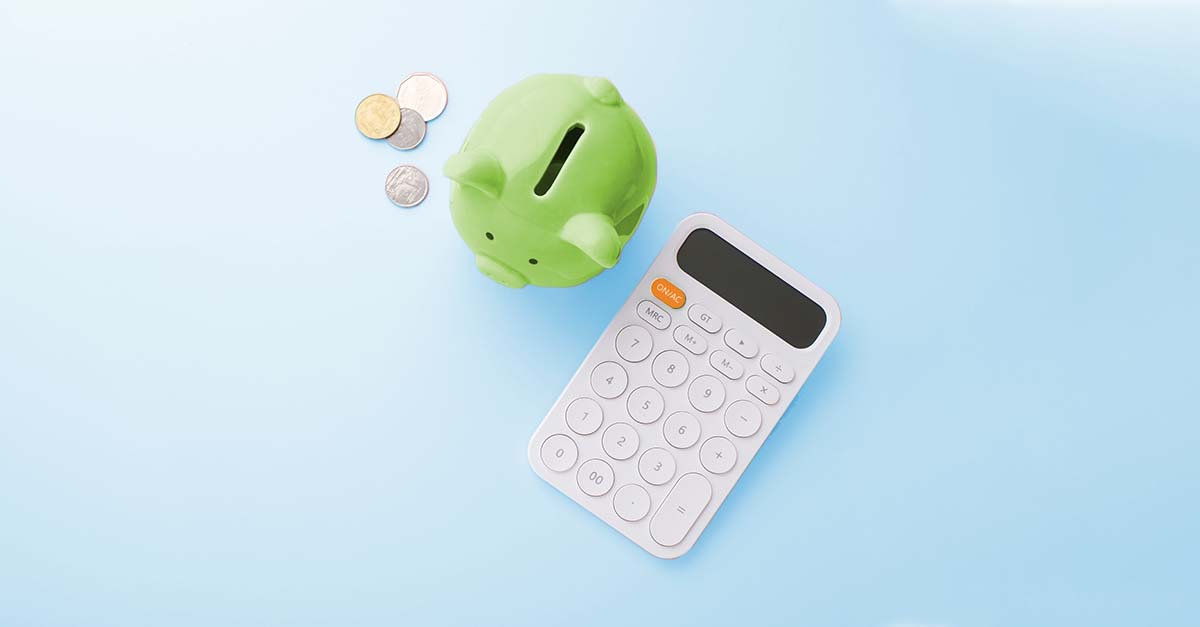
Is ERP Worth the Cost? A Complete Guide to ERP ROI
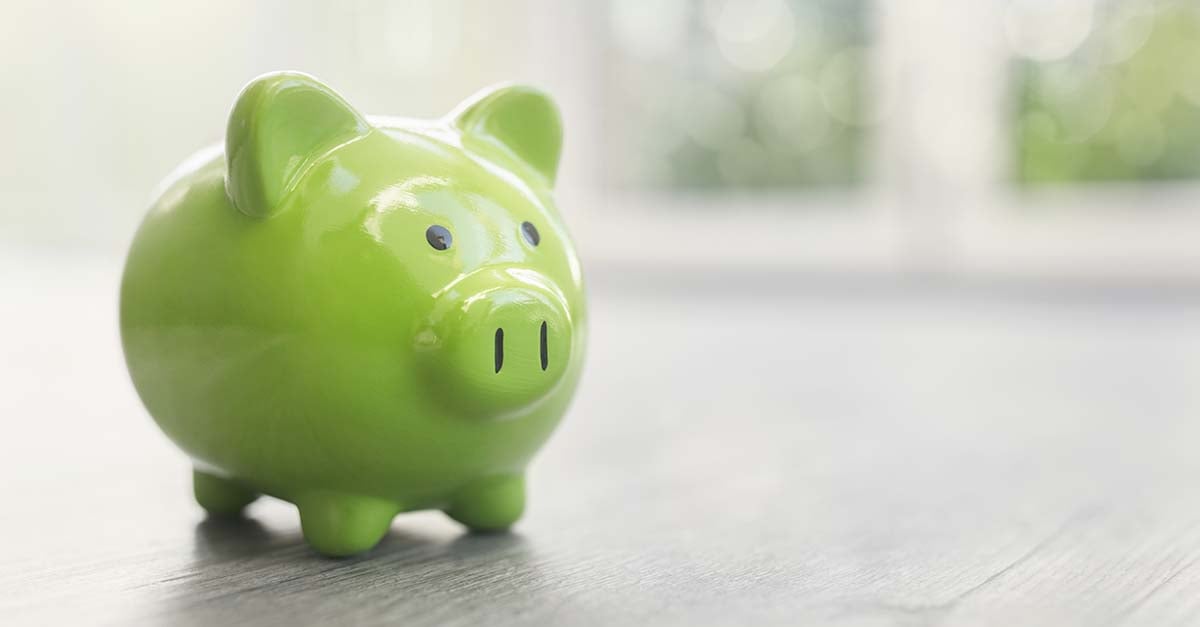