Blog
Share this
Leveraging Your ERP for Manufacturing Capacity Planning
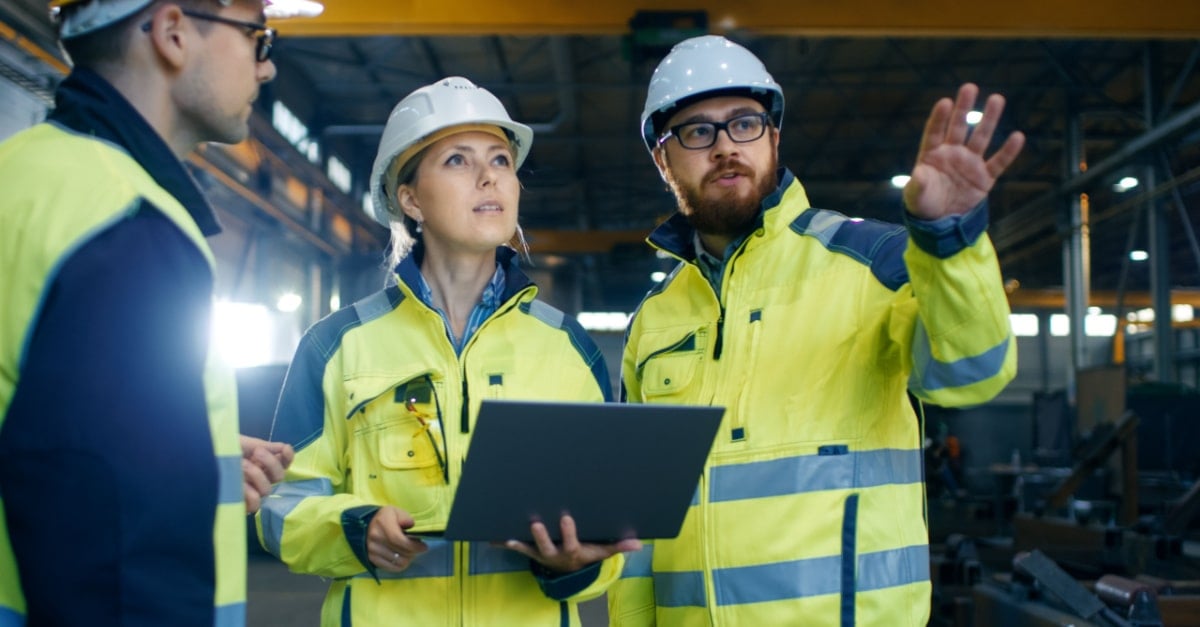
by Jalene Ippolito on July 05, 2023
As individuals, we perform best when we recognize our strengths and assess our capabilities. The same is true for manufacturing companies.
A thorough assessment of the maximum production capacity—not just a rough estimate—allows them to perform optimally.
Production efficiency is crucial for manufacturers to reduce costs and improve profitability.
Manufacturing capacity planning is a meticulous process that allows manufacturers to optimize resource utilization, eliminate waste and maximize production output.
In this article, we'll look at how an integrated ERP solution enables small and medium manufacturing companies to optimize their production capacity.
What is capacity planning in manufacturing?
Capacity planning in manufacturing involves assessing the maximum production output possible for a given production facility at a given time.
Capacity planning helps manufacturers determine the production capacity required to meet the demand for goods or services. By analyzing the highest possible production rate and aligning it to the market demand, they can create a plan to maximize actual output.
Manufacturers can significantly lower production costs by streamlining operations and eliminating inefficiencies, which translates directly into higher profitability.
At ProjectLine, we work with manufacturing companies to streamline operations and improve efficiencies. Click here to read more on this.
Why is manufacturing capacity planning essential?
In today's highly competitive business landscape, manufacturers must constantly strive to maintain a competitive edge—and one of the ways to do that is to produce goods more efficiently, offer competitive pricing and meet market demands promptly.
Production efficiency is crucial for manufacturers as it drives cost reduction, improves profitability, enhances competitiveness and satisfies customer demand. By continually striving for higher efficiency, manufacturers can achieve operational excellence and position themselves for long-term success in the dynamic and evolving business landscape.
For example, if a manufacturing company plans production based on rough estimates rather than meticulous planning, they may produce larger volumes than the market demand. Offloading that excess inventory at a discount means sacrificing profit margin. At other times, they may not produce enough volume, leading to lost revenue and potentially lost customers if they’re continually short on product. They may even take on more orders than they can fulfill, resulting in delivery delays and customer dissatisfaction.
So, accurately assessing your manufacturing capacity ensures that you take on the right amount and size of orders that you can fulfil promptly, which translates to satisfied customers and a good reputation for your company.
Pro tip
Watch this video demo of how NetSuite ERP handles demand and supply planning.
What are the benefits of manufacturing capacity planning?
Effective capacity planning provides numerous benefits that impact the company's revenue.
Efficient production
Accurate capacity planning improves production scheduling, reduces bottlenecks and minimizes idle time. Improved production floor output reduces lead times and ensures on-time delivery of products. This, in turn, boosts customer satisfaction, strengthens customer relationships and positively impacts revenue.
Better resource utilization
Capacity planning optimizes your utilization of resources, namely machinery, labour and materials. It helps you minimize resource wastage, control production costs and improve production efficiency. This streamlined resource utilization translates into higher profitability and increased revenue.
Adapt to demand fluctuations
Well-defined capacity planning allows you to adapt quickly to fluctuations in customer demand or changing market conditions. You can scale up production to take on larger orders during peak season or when demand is high, and scale down during the slack season.
Eliminate the risk of stockouts and excess stock
Good capacity planning can prevent overproduction and underproduction. Excess inventory leads to a rise in costs, which negatively impacts profitability. Underproduction can lead to stockouts and loss of revenue-generating opportunities.
Derive strategic insights
Capacity planning gives you valuable insights for long-term planning, such as when to scale up production capacity, how to optimize the use of existing resources or even when to invest in new resources—for example, acquire more warehouse space, employ more workers and so on.
These benefits streamline revenue generation and ultimately result in a better customer experience and more growth opportunities for your manufacturing company.
While you can use manual worksheets for capacity planning, a manufacturing ERP is the best way to streamline your capacity planning process.
In the next section, we look at how adopting ERP software enables more accurate capacity planning.
How ERP for manufacturing enables accurate capacity planning
Here's how a manufacturing ERP enables efficient capacity planning:
Enterprise-wide data visibility
An ERP, by definition, is an enterprise-wide system—which means it integrates data from various departments and processes. The ERP, therefore, is a centralized database of real-time information that provides high-level visibility and a holistic view of the entire company's operations. This visibility is critical for capacity planning which is based on accurate and real-time data about inventory levels, resource availability, production schedules and orders logged into the system.
Forecasting & demand planning
A manufacturing ERP includes specific demand forecasting and planning functionality. It predicts future demand by analyzing historical data, order information and external market trends. This information is very useful for capacity planning so that you can align decisions about production capacity with anticipated demand and manage resources optimally.
Production scheduling
A manufacturing ERP keeps track of and manages resources such as materials, inventory machinery, equipment, workforce, etc. Real-time updates and notifications in the ERP system enable planners to adjust production schedules based on expected demand.
Reporting
ERP offers strong reporting capabilities that allow users to track and monitor the company's production efficiency, capacity utilization and resource performance. This helps identify areas of improvement and proactively revise capacity plans.
ProjectLine's ERP experts help you leverage manufacturing ERP software such as SAP Business One and NetSuite, complete with the features mentioned above, to enable accurate manufacturing capacity planning.
Leveraging ERP for accurate & effective capacity planning
Accurate capacity planning starts with having the right systems in place. ERP can give you the real-time visibility and planning tools you need—but only if it’s the right fit for your business today.
If you’re not sure whether now’s the time to invest in ERP, take our quick ERP Need Assessment. In just 5 minutes, you’ll get a personalized report showing how much your manufacturing business needs ERP and what your best next steps are.
Share this
Stay in the Know!
Join other SMEs who receive our monthly ERP insights, tips and best practices.
You may also like
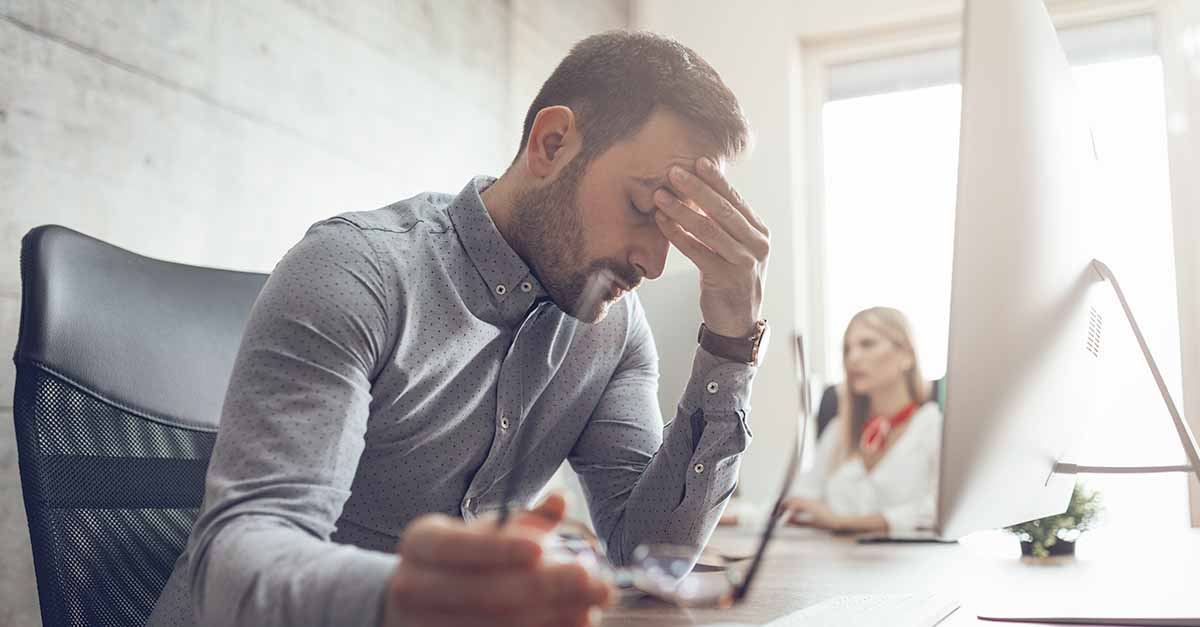
5 Ways Disparate Systems are Costing You
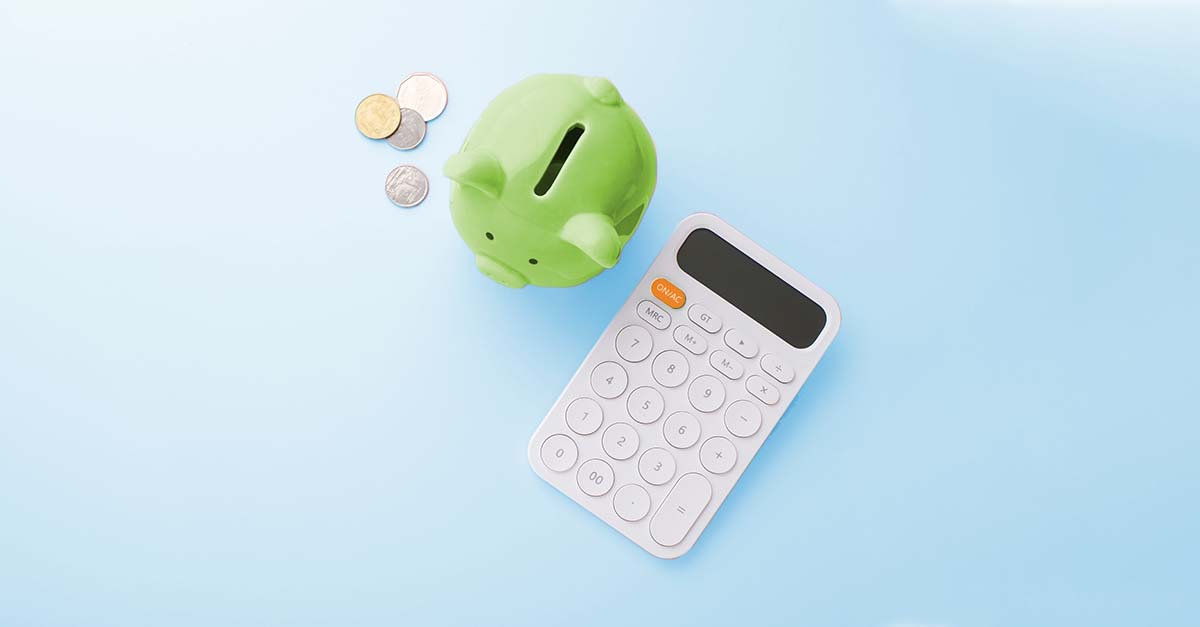
Is ERP Worth the Cost? A Complete Guide to ERP ROI
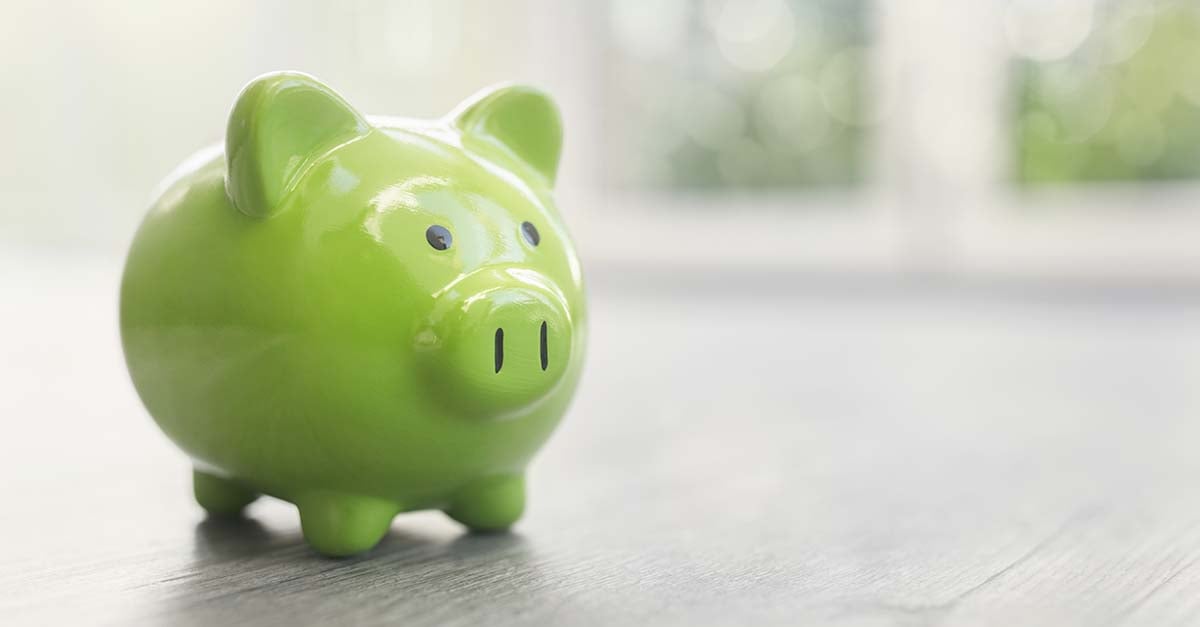