Blog
Share this
What is MRP? Do Small to Mid-size Manufacturers Need it?
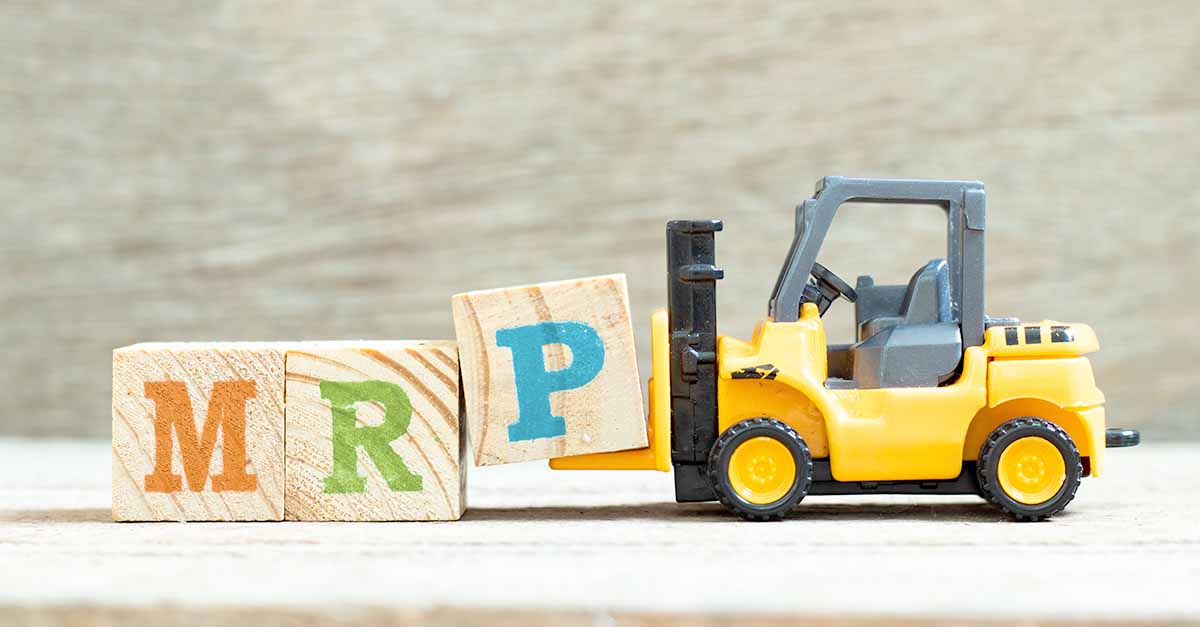
by Gerwyn Begonia on November 05, 2020
MRP (or Material Requirements Planning) is a system for calculating the materials and components needed to manufacture a product. In short, it helps you plan what you need to purchase or produce to make sure manufacturing can meet demand efficiently. Sounds simple enough, right?
The process itself is actually fairly complex. MRP uses forecasting to determine customer demand for finished products (called independent demand), then in turn forecasts the quantities for components, parts or sub-assemblies (called dependent demand) to produce the final product. There are three basic questions to ask throughout the process:
- What materials and components do we need? These are the items that make up your Bill of Materials (BOM).
- How many of each material / component do we need? When determining the quantity to be purchased or produced, you’ll factor in quantity on hand, open purchase orders, planned for manufacturing and already committed to existing orders.
- When do we need the components? This will determine the schedule to purchase or produce the items.
Benefits of MRP for SMEs
So, how does MRP help your business? Put simply – both distributors and manufacturers can use it to ensure they have the right items in stock based on required quantities.
In a manufacturing scenario, it helps you keep your production schedule on track by ensuring the right materials and components are available when needed. More accurate production planning and scheduling help to optimize your labour and equipment usage, leading to improved manufacturing efficiency overall. It also allows you to minimize stock-outs and reduce inventory costs by purchasing or producing the optimal amount and type of inventory based on your production needs. All this combined helps reduce lead times, contributing to improvements in customer satisfaction.
Similar benefits apply for distribution companies – MRP helps you optimize purchasing based on demand to ensure you have the right quantity of the right products at the right time. Not only does this improve your customer experience, but it can also lower inventory carrying costs.
Is MRP right for my business?
As a small or mid-size business, you might find yourself thinking that MRP is only for the big players. But it might be a good fit if you have hundreds (or even thousands) of customers, a significant order volume and hundreds of items to manage. Consider this scenario – you have to figure out what to purchase or produce based on hundreds of orders, factoring in product lead times, min-max inventory levels and minimum purchase levels for hundreds of items. How do you do that manually? And are you able to plan with a reasonable degree of accuracy?
If that sounds familiar, it’s worth considering MRP as a solution. You could be in the process of evaluating ERP solutions and identifying your requirements, or perhaps you have an ERP system but aren’t using the MRP functionality. Whatever your starting point, ask these questions among your team to uncover whether you need MRP. Each question you answer “No” or “I’m not sure” to is an indicator that you could benefit from Material Requirements Planning.
- Do we have enough inventory to meet customer demand?
- Can we forecast what we should buy based on historical sales?
- Are we losing potential sales?
- What’s our backorder rate?
- Can we deliver product on time?
Do we need MRP or ERP?
It really comes down to your business needs. But if you have plans to grow your business and want to achieve the greatest return in terms of efficiency and visibility, ERP (Enterprise Resource Planning) is probably your best bet. A stand-alone MRP solution only addresses that one business need and has limited value if not connected to the live inventory, production, sales and purchasing transactions that a complete ERP solution offers. An ERP system incorporates your entire business into a single system – including MRP – allowing you to see improvements across the company, not just in planning. Also consider that MRP is most successful when the accounting side is accurate, which is easiest to achieve when MRP is part of your larger ERP solution. In the end, you’ll reduce duplicate information and increase efficiency at scale.
If these points have you leaning toward ERP, the next step is to confirm whether it is the right move for your business right now. To truly gauge your readiness, take our ERP Need Assessment. This quick and insightful tool will help you identify gaps in your current operations and provide clarity on whether your business is ready for the transformative impact of ERP. Don’t just guess—get a clear picture of what’s next for your business.
Share this
Stay in the Know!
Join other SMEs who receive our monthly ERP insights, tips and best practices.
You may also like
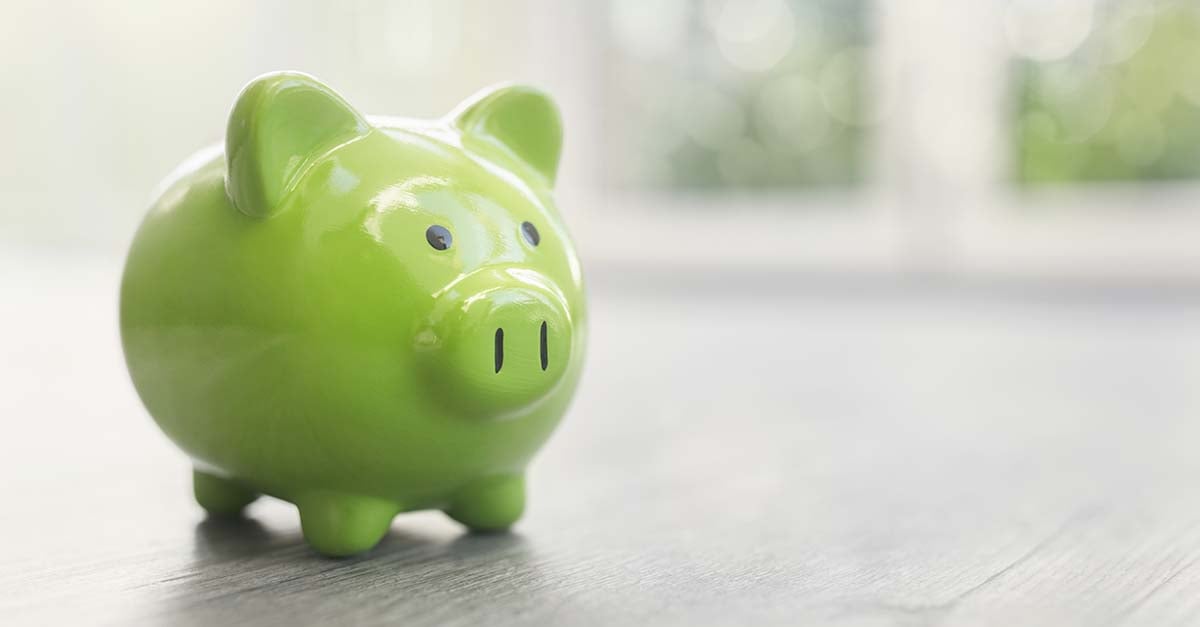
The Complete NetSuite Pricing Guide
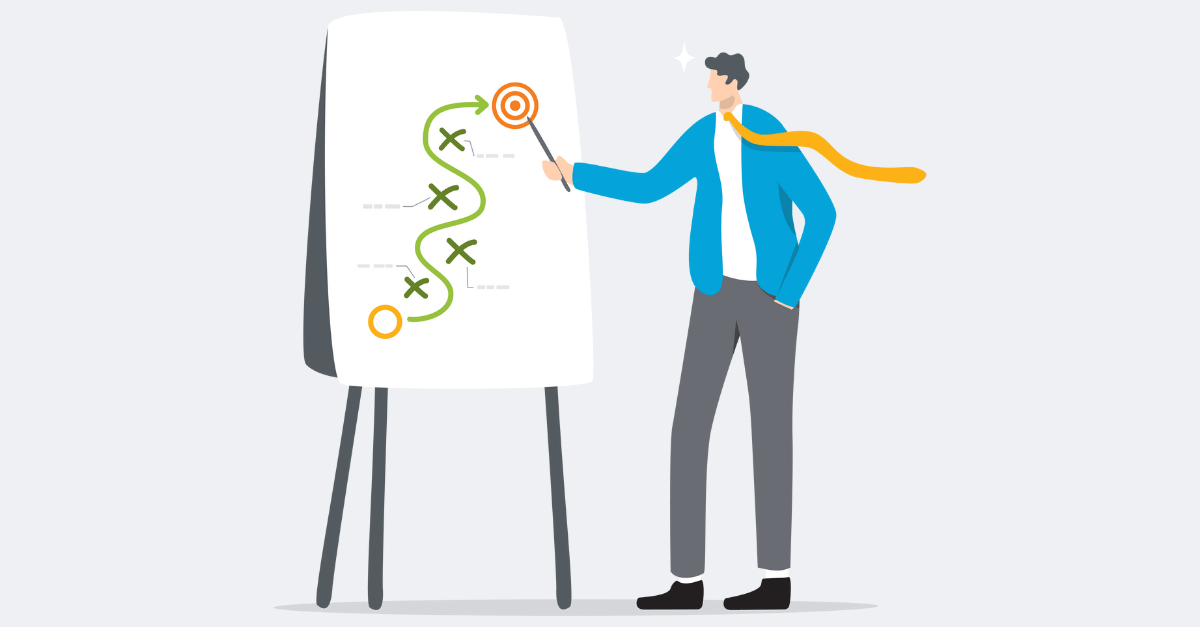
Choosing ERP? Don’t Fall for These Common Sales Traps
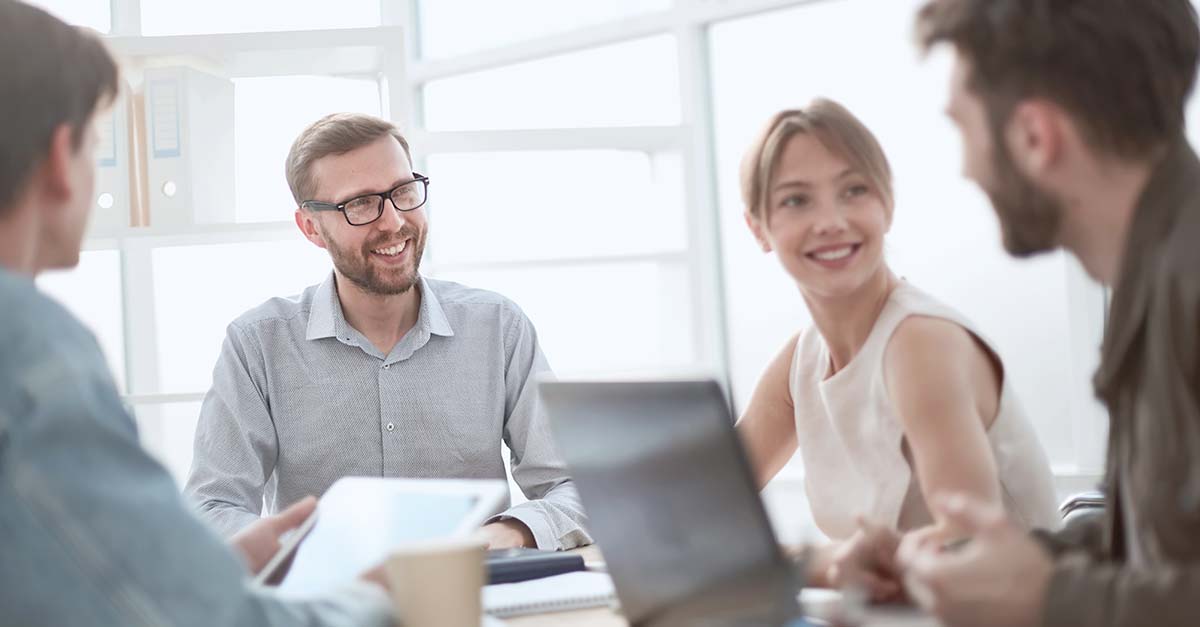