Blog
Share this
Navigating Supply Chain Challenges
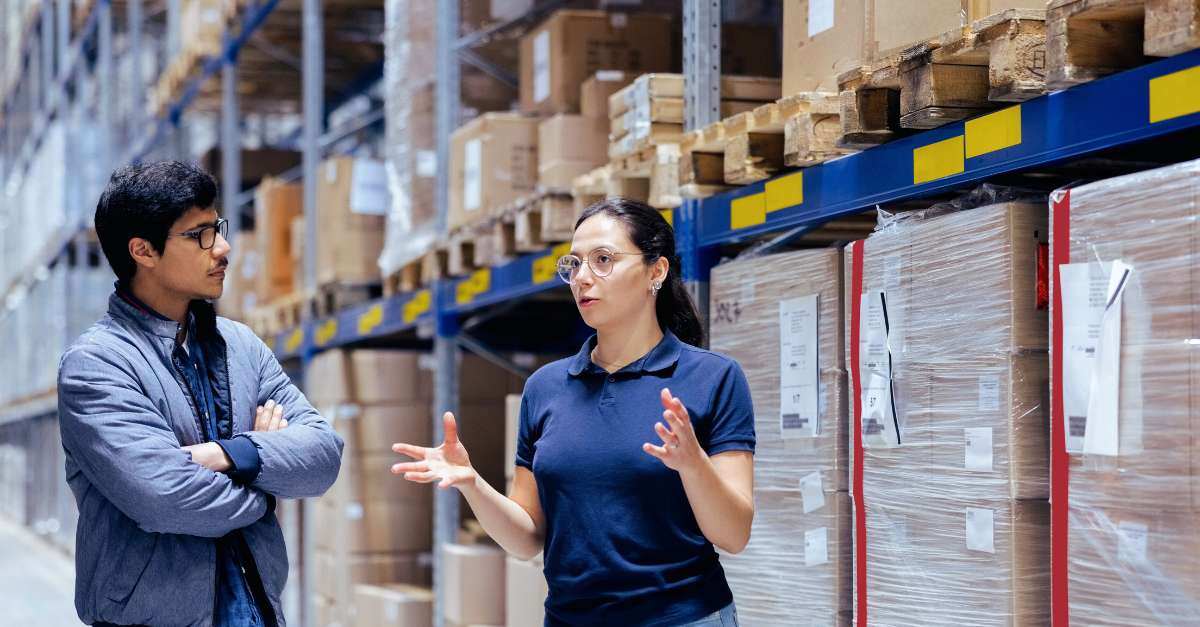
by Carly Caines on July 09, 2024
A strong supply chain isn’t just about efficiency—it’s about being prepared for anything. Imagine having just the right amount of inventory, forging strong ties with suppliers who deliver quality on time and being nimble enough to handle unexpected curveballs like shipping delays or sudden spikes in demand. When your supply chain is on point, you can move goods faster, keep costs down and stay ahead of the competition.
In this blog, we'll explore strategies and tools for building resilient supply chains, overcoming challenges like inventory management and demand forecasting, and introducing a revolutionary supply chain management technology. Get ready to sail through the highs and lows of supply chain management—it's going to be a ride worth taking!
What is supply chain management?
Supply chain management is how businesses handle all the steps involved in getting their products or services from suppliers to customers.
It's like a big network of companies, processes and resources that work together to make sure everything flows smoothly. This includes everything from sourcing raw materials, manufacturing products, storing them in warehouses and delivering them to customers.
Supply chain management is crucial for businesses to stay competitive and keep customers happy by ensuring products are available when and where they're needed, all while keeping costs under control.
Why is supply chain management important?
A strong supply chain is more than just moving stuff around efficiently. It's also about planning ahead so you have the right amount of inventory without over-or-under-doing it. It also considers building strong relationships with suppliers and making sure they deliver quality goods on time. Plus, a strong supply chain involves being flexible and able to quickly adapt to changes in demand or unexpected events, like disruptions in shipping or shortages. When you manage your supply chain well, things run smoothly—you can move goods faster, keep just enough inventory and avoid problems.
However, ineffective supply chain management can lead to stockouts, late deliveries and higher costs from inefficiencies, which negatively impact customer relationships and make it harder to compete. To maintain stable operations and keep growing, investing in good supply chain strategies is essential.
Common supply chain challenges
Supply chain management requires a balancing act of many moving parts. Here are some of the most common challenges businesses face:
Managing inventory levels
Managing inventory levels can be a real balancing act and a big challenge in supply chain management. On the one hand, you want to make sure you have enough stock to meet customer demand, but on the other hand, you don’t want to overstock and tie up a bunch of cash in excess inventory. It’s like walking a tightrope – lean too much in one direction, and you risk stockouts and lost sales; lean too much in the other direction, and you’re stuck with high holding costs and potentially obsolete products.
Cost fluctuations
Cost fluctuations are a real and unavoidable headache for distributors and manufacturers. One day, your raw materials might be affordable, and the next, prices skyrocket due to market shifts, political events or natural disasters. This unpredictability makes it tough to keep product costs stable and can eat into your profit margins.
Freight costs can also be another wild card. Shipping rates can vary widely due to fuel price changes, labour shortages or global events (such as a strike or pandemic). When freight costs suddenly spike, it will inevitably throw off your budget. This makes it hard to ensure timely customer deliveries, impacting your reputation and customer satisfaction.
Complicated demand forecasting
Trying to accurately predict customer demand is no easy feat, especially with so many factors at play—like market trends, seasonal changes, economic shifts and unexpected events like natural disasters or political upheavals. When these forecasts miss the mark, you can end up either overestimating or underestimating demand. This complexity also disrupts production schedules and puts a strain on supplier relationships. If your business is constantly adjusting orders based on fluctuating forecasts, suppliers may struggle to keep up, leading to delays and potential quality issues.
Lack of visibility
One of the best ways to tackle supply chain challenges is to spot them early, which can be tough without clear visibility into your operations. Without good visibility, it's tough to forecast demand accurately and manage inventory levels. You might end up overstocking, which ties up capital and increases holding costs, or understocking, which leads to stockouts and missed sales opportunities. Both scenarios hurt your bottom line and frustrate customers.
Limited visibility also makes it hard to spot and address problems quickly. If a shipment is delayed or a supplier has an issue, you might not find out until it's too late. This can lead to production halts, increased costs and delayed deliveries, all of which can harm your business.
Data sharing
Different parts of the supply chain often use different systems and formats, making it tricky to get everyone on the same page. It’s like trying to complete a puzzle with pieces from different sets. This lack of seamless data sharing can lead to miscommunications, delays and errors. For instance, if your supplier isn’t sharing inventory levels or shipment statuses in real time, you might have stocking issues and order delays. To overcome this, you must invest in integrated systems and foster a culture of collaboration and transparency across the supply chain.
5 strategies for building a resilient supply chain
Creating a resilient supply chain is essential for today’s dynamic and often unpredictable market conditions. Here are some key strategies to ensure your supply chain can withstand disruptions and stay efficient.
1. Enhance inventory visibility
Centralizing data is a crucial step to improve inventory visibility. By having all your inventory information in one system, you eliminate data silos and make sure everyone has access to the same accurate information. With centralized data, decision-making is quicker and more informed, with fewer errors along the way.
Additionally, consolidating data from across the organization in an ERP system provides data insights that are tough to achieve through manual analysis. You can use historical data to spot trends, while monitoring current performance with real-time KPIs. This combination allows for better forecasting, more effective inventory management and the ability to respond swiftly to changes in demand.
2. Diversify supplier base
Relying on a single supplier for critical components can be risky. Diversifying your supplier base and having contingency suppliers in place reduces the risk of supply chain disruptions. If you encounter issues with one supplier, you can default to an alternative, ensuring a steady flow of materials and minimizing downtime.
It’s also important to regularly track and measure supplier performance. By monitoring key performance indicators such as delivery times, quality and responsiveness, you can identify potential issues early and maintain a reliable supply chain.
Moreover, developing long-term relationships with key suppliers can pay off in the long run. Good relationships foster trust and collaboration, leading to better communication, favourable terms and increased reliability. These partnerships can often result in suppliers prioritizing your orders, offering better prices and providing valuable industry insights.
3. Address risk
Addressing potential risk is essential for maintaining supply chain resilience. With a comprehensive risk management plan, you’ll be prepared for disruptions like natural disasters, supplier issues, or geopolitical tensions. By identifying risks early and having contingency plans in place, you can minimize the impact of disruptions and keep your supply chain running smoothly.
4. Improve operational efficiency
Adopting lean practices focuses on minimizing waste and maximizing value in your supply chain processes. It’s worthwhile to streamline operations, reduce excess inventory and optimize workflows to improve efficiency and reduce costs. Lean practices also encourage continuous improvement, ensuring your supply chain remains agile and responsive.
Investing in employee training and development is also important. A well-trained workforce, equipped with the latest industry knowledge and best practices, can handle complex supply chain challenges more effectively, boosting performance and productivity.
5. Leverage technology
Using the right technology is key to building a resilient supply chain. Technology ERP software can play a critical role by providing visibility tools, automation and analytics that enhance decision-making. This technological integration improves efficiency and helps you proactively manage supply chain challenges, ensuring your business remains competitive and resilient.
The role of ERP in supply chain management
Enterprise Resource Planning (ERP) is a category of software that helps your business manage and integrate essential operations. Think of it as a central hub where different parts of your business—like purchasing, inventory, sales, finance and production—can all share data and access important information. This integration makes your operations run smoother, data more accurate and decision-making easier.
When it comes to supply chain management, ERP is a game-changer. It keeps everything running smoothly from the moment raw materials are ordered to when finished products are delivered. ERP will become the backbone of your business by providing real-time updates on inventory levels, production schedules and shipments. It will help your business avoid stockouts, reduce delays and improve overall efficiency. Plus, ERP makes it easier to forecast demand, manage suppliers and control costs, ensuring your business can quickly adapt to any changes in the market or customer needs.
Benefits of ERP for supply chain management:
ERP systems are like the Swiss Army knives of business software—they provide a full range of benefits that will help optimize your supply chain. Here are the top benefits:
- Effective demand planning
- Improved inventory and warehouse management
- Fewer production bottlenecks
- Greater visibility into supply chain performance
- Better supplier relationships
Now that you’ve gotten a good grasp on navigating the wild world of supply chain management, it’s time to put these strategies into action and reap the rewards.
Picture this: with ERP by your side, you’ll be rocking effective demand planning like a pro, keeping your inventory on point without the headache of overstocking or running out. You can also say goodbye to those pesky production bottlenecks and hello to smoother operations! Plus, don’t forget the easy access to real-time reporting on all aspects of your business so that you can make quick and effective decisions.
Take our easy, 20-question ERP Need Assessment to find out if ERP is the right next step for your business. It’s quick and free—and you’ll get a personalized report with recommendations based on where your business stands today.
Share this
Stay in the Know!
Join other SMEs who receive our monthly ERP insights, tips and best practices.
You may also like
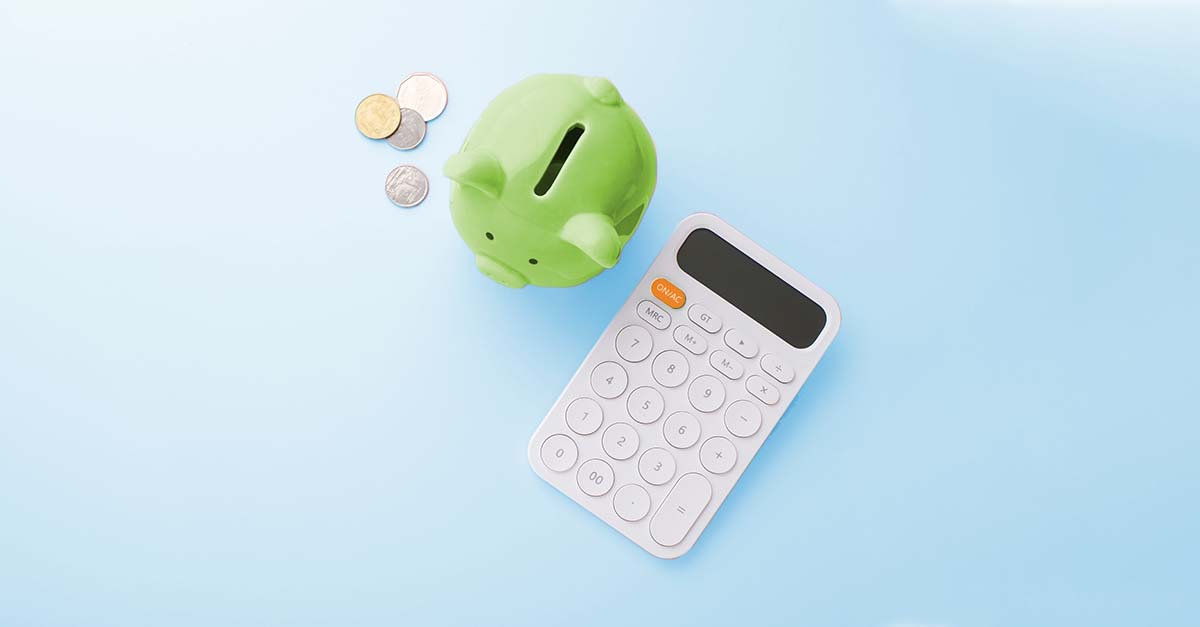
Is ERP Worth the Cost? A Complete Guide to ERP ROI
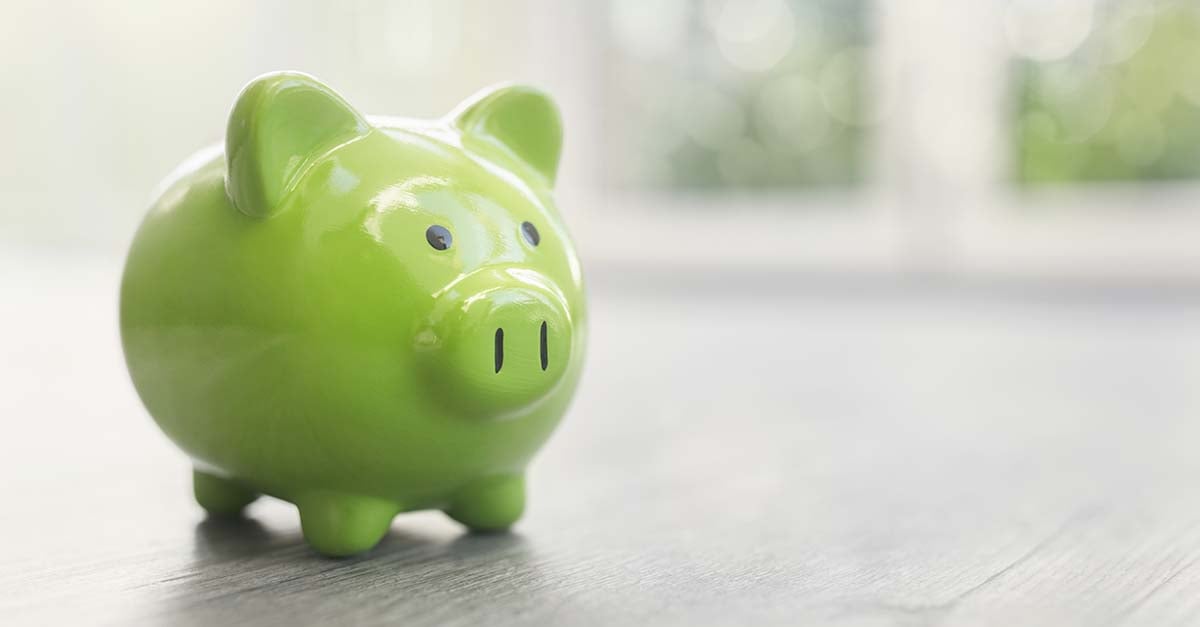
The Complete NetSuite Pricing Guide
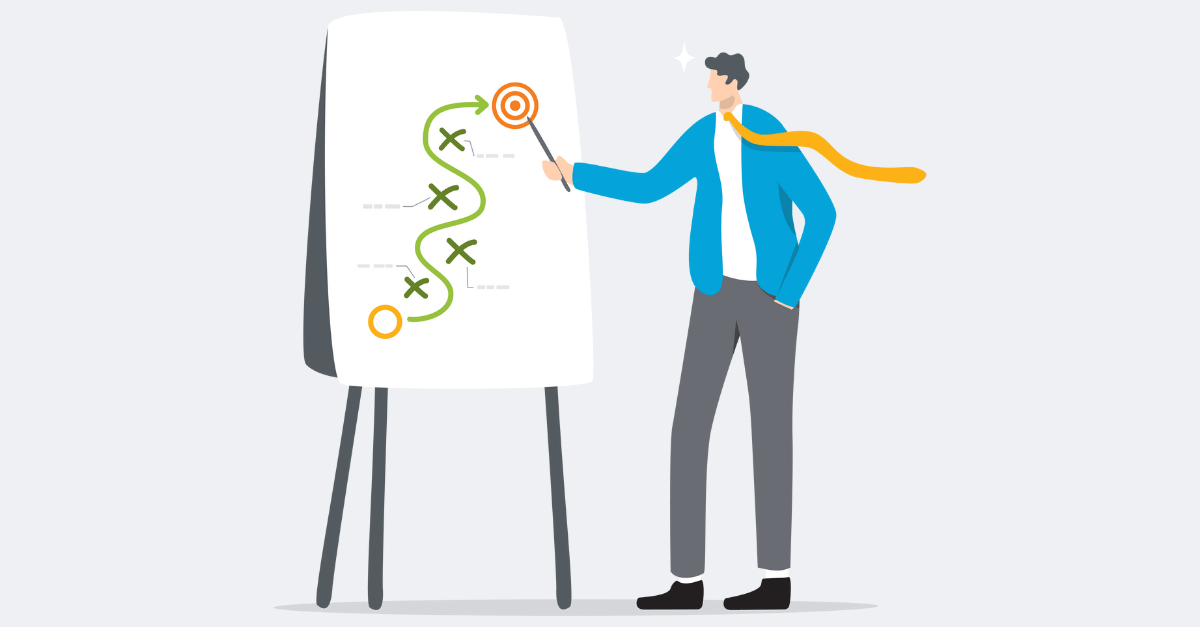